Gas Turbines
Learn about the history and development of the gas turbine
The gas turbine has become an important, widespread, and reliable device in the field of power generation, transportation and other applications. A gas turbine is an internal combustion engine, it can burn a variety of fuels (which contributes to it's great versatility).
Uses of gas turbines:
There are many forms of gas turbines from 1 to 10+ meters in length. Gas turbines come in a great variety of forms to fulfill a variety of power needs from driving tanks, jets and helicopters to power generation and industrial power uses.
In this webpage we discuss gas turbines used to make electric power.
Later on you can learn about the many other complex forms of the gas turbine listed on the wiki page.
1.
How it Works
2. Brief History of Gas Turbines
3. Gas Turbine Development at General Electric, by Arne
Loft
4. Gas Turbine Control Systems
1. How it Works:
The gas turbine is used to make mechanical energy from a combustible fuel. In the gas turbines used to make industrial/electrical power the mechanical energy comes in the form of a rotating shaft (as opposed to pressurized thrust of a gas turbine jet engine). This shaft has an enormous amount of power and torque.
Uses of a gas turbine with shaft:
The shaft can be connected to other machinery to do various types of work such as: turning a helicopter rotor, running a compressor (which "crushes" a gas to a condensed form for use in industrial applications) or generating electric power.
The gas turbine is useful to our modern world because it is relatively compact in size and makes a lot of power. Gas turbines are used in backup power systems in Manhattan for example, when the grid goes down due to natural disaster, gas turbines power up and can produce power for emergency uses.
Gas turbines are used on oil platforms to make power. The oil platform is like a small city, isolated out on the water, so it requires a lot of power and does not have a lot of space. Gas turbines are also used in oil refineries to make power for the cracking process.
Harnessing the power of an explosion: How the device works:
Original graphic above: General Electric.
The gas turbine burns fuel in a high pressure combustion chamber, the products of this are forced into a turbine. A turbine has specially engineered blades attached to a central shaft, and as the high pressure gasses flow through, the shaft rotates. The shaft spins with incredible force. The shaft is often connected to a generator which creates electric power. Sometimes the shaft is connected to a compressor. Compressors are used to compress gas or vapor for a myriad of industrial and commercial uses.
Watch the video below to learn details on how the gas turbine works:
2. Gas Turbine Brief History:
Gas turbines developed from two fields of technology: the steam turbine, and the internal combustion engine. Work on both of these fields helped lead to the "Modern Gas Turbine" of the post 1940's period.
1500 - 1870s: Leonardo da Vinci, Gionvanni Branca, John Barber, and others mention or design devices that use hot gas or steam to create motion. Simultaneously work by Samuel Brown, Sadi Carnot, Samuel Morel, William Barnett, and others develop the design of the internal combustion engine. Basic understanding and theory of how gases burn and behave in enclosed spaces is developed.
![]() The Steam Turbine by GE, click on the image to see a larger photo |
|
Jet engines use gas turbine technology. This application of gas turbines was developed first by Sir Frank Whittle, Hans von Ohian, Dr. Franz Anslem, and more from the 1930-42 period. Jet engine development is another topic best discussed in a separate page.
The first modern Gas Turbine:
BCC Brown Boveri & Cie (Switzerland) conducts development of gas turbines for utility power generation starting in the 1930s. Raul pateras de Pescara , Hans von Ohain, Max Hahn develop their own designs outside of BCC Brown Boveri. In 1936 BCC Brown Boveri built a supercharged velox boiler for a refinery in Pennsylvania which was used in the catalytic cracking process for oil. In 1939 a 4 Megawatt power generation gas turbine is installed in Neuchatel, Switzerland. You can now see this turbine on display at Birr, Switzerland. It ran from 1939-2002.
The first commercially sold gas turbine in the Western Hemisphere used for electric power generation was installed in 1949 at Belle Isle Station, Oklahoma, US. A core group of engineers from General Electric pioneered an efficient and power design that formed the basis for a multi-billion dollar industry. The design led to an explosion in sales of gas turbines worldwide. Gas turbines finally had established a firm place in reliable power generation after 1950.
Pioneers of the 1949 gas turbine at GE include: Bruce Buckland "Mr. Gas Turbine", Neal Starkey (GT Control Genius), Arne Loft*, Andy Smith, Bob Kramer, Bob Hendrickson*, Dick Noe, Tom McKone, Al Boiko, Bill Taylor, Goldy Goldsworth, Frank Yeaple, George Fusner, Eddie Ouimet, Andy Dargis, Roy Linn, John Bak, Phil Bell, Fred Cummings, Fernand Pomerleau.
*Video lectures are available of Arne Loft and Bob Hendrickson
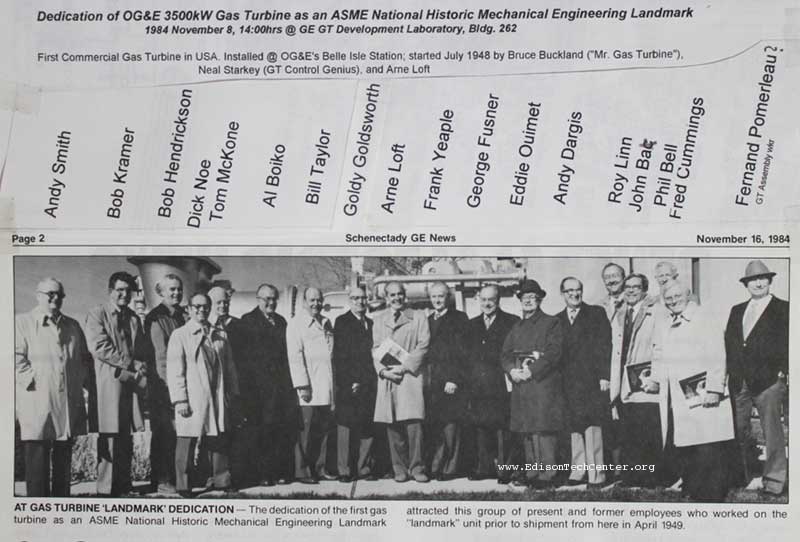
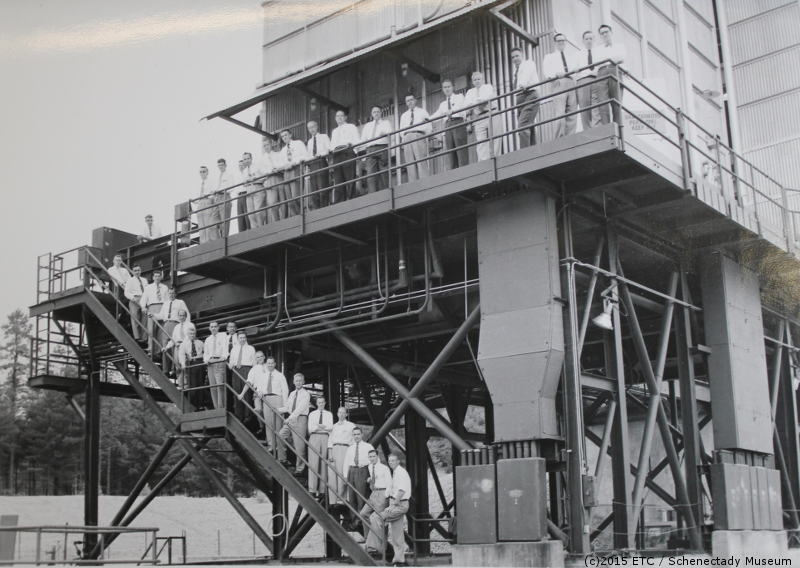
Above: Rocket and gas turbine engineers at Malta Test Site
4. Gas Turbine Control Systems:
Gas turbines are extremely sophisticated devices which require precise controls to operate. Control engineers at General Electric were the first to design a reliable control system. Neil Starkey designed a mechanical control which was reliable in the 1940s. A better system was needed using computers and electronics (which itself had just been developed at the time). This first electronic system was developed by Arne Loft, a mechanical/electrical engineer working at GE in Schenectady, New York. Below is his story of the development of the first Speedtronic Control System. (Later on Speedtronic became a large product line which controls more than just gas turbines, but steam turbines and other devices).
Video on the first Speedtronic Control System below:
1980s:
The 7 F Gas Turbine by General Electric (video Youtube):
Related Topics:
![]() Diesel Electric Locomotives |
![]() Steam Trains |
![]() Electric Cars |
![]() Trolleys and Light Rail |
![]() Steam Turbines |
![]() Dynamos and Generators |
Sources:
-History of the
Gas Turbine with Bob Hendrickson by Frank Hackert and the Edison
Tech Center
-The Edison Presents: Interview with Arne Loft by the Edison
Tech Center
-Wikipedia (Internal Combustion Engine, Gas Turbine entries)
-About.com Inventors
-The General Electric Story by the Hall of History
- ASME.org -Belle Isle Gas Turbine
- The ABB Group, History web page